The user interface will be consistent with the existing 3DCS Variation Analyst based user interface. This is a separately licensed product. If any of the 3DCS FEA CM functions are accessed, the add-on license is activated. When a compliant model is opened the specific license is automatically checked out.
Creating a Compliant Model-Typical user scenario
1. | 3DCS Variation Analyst Based - Model Creation |
a. | Start with a completed 3DCS model utilizing the standard Moves, Measures, and Tolerances and/or FT&A, exactly the same as the existing 3DCS modeling process. |
b. | Determine which parts in the rigid body model will be simulated as compliant or flexible parts. |
c. | On these compliant/flexible parts, create additional DCS modeling points at all locations desired for any additional clamp or weld locations that cannot be used in the standard rigid body moves. Create any additional DCS modeling points in locations on compliant parts where visual bending is desired and additional measurements will be taken. |
2. | Export CAD Data that will be used to create the mesh for each part. |
a. | Export CAD (.igs / .stp) files for each compliant component. |
3. | Using an FEA meshing package, along with the newly created IGES or STP files, create a mesh file for each of the compliant parts (see 3DCS_FEA_Compliant_Modeler on Community). |
4. | 3DCS Variation Analyst - FEA Data Linking |
a. | Launch 3DCS Variation Analyst software with 3DCS FEA Compliant Modeler. |
b. | Create an Load FEA Data move and load the following files for each compliant part: |
b.1) | Stiffness Matrix (*.bdf, *.pch, *.mtx, *.dmig, *.lis) file(s). |
b.2) | Mesh (*.nas, *.blk, *.inp, *.fem, *.bdf, *.cdb) file(s). |
b.3) Mass Matrix (*.bdf, *.pch, *.mtx, *.dmig, *.lis) file(s). - if applying gravity.
Notes:
•Once the mesh and stiffness files are loaded, a Nominal Build is required to link the ASETs from the mesh files to the modeling points for each part.
• Validation checks are added to notify the user whether there is no FEA data, or whether there is FEA data, but it is not valid.
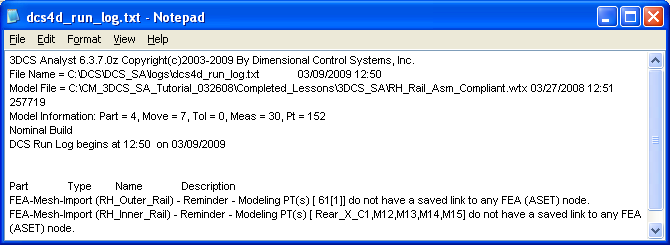
c. | Use FEA Point Linking to verify if DCS modeling points are linked to the FEA mesh nodes, and manually link them, if necessary. |
5. | 3DCS Graphical and Statistical Analysis. |
b. | 3DCS Animation and Deviation will function identical as in a standard 3DCS Variation Analyst version. |
| If the over-constrained compliant parts parts do not deform during Nominal Build, Animation, or Deviation, use the Update DCS CGR with the Minimum Segment Number check-box active; this setting is based on the mesh density and the CGR will have more tessellation and deform accordingly. |
c. | DCS Points and Mesh will deviate based on all DCS Tolerances, Rigid Moves and Compliant Routines. |
d. 3DCS Analysis will function identical as in a standard 3DCS Variation Analyst version.
Important!
Although compliant moves are said to apply constraints to the object part, the compliant move constraints are only recognized by other compliant moves and are ignored by any subsequent rigid moves. A rigid move following a constraining compliant move can change the position of the part. Therefore, creating rigid moves after compliant moves should typically be avoided.
If a rigid move must come after a compliant move, the move should be located at the assembly level that includes/contains all the object parts previously constrained together by compliant moves.